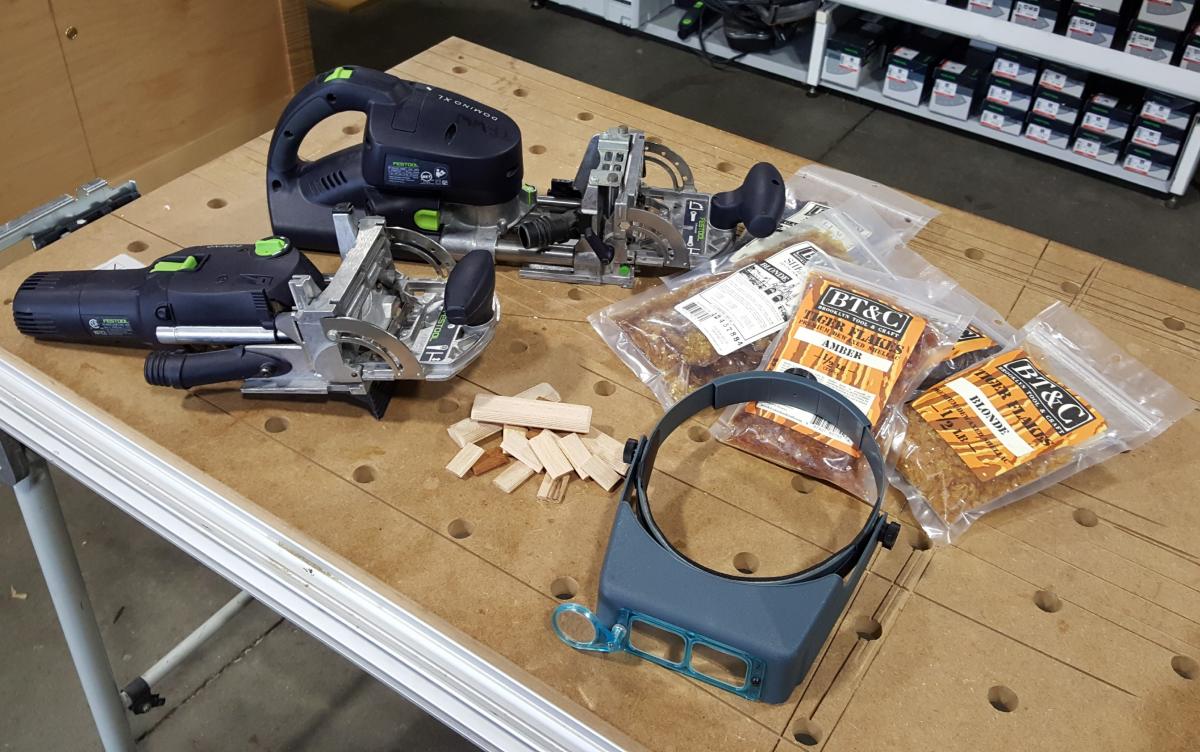
This is part two. Part 1 is here.
I've been working with wood since I was a kid. I took my first woodworking class at the 92nd Street Y when I was 6 years old. I've been taking classes and building stuff for over 35 years. For the last 17 I have been working at Tools for Working Wood. In that time, new tools and new techniques have come on the market. By and large I have ignored them in my personal work. However, I haven't ignored everything, and my methods of work have in certain areas changed dramatically for the better. I've broken up my list of ten things into three posts so I don't drone on and on here.
Domino Joiner
When I studied in school, the idea of a powered joining system was an anathema to teachers and students of traditional methods. At the time, there weren't many options -- dowel joints were the most prominent. The Metropolitan Museum's Study Collection had Frank Lloyd Wright chairs that used dowel joints to hold the backs together. What made me notice this? The chairs were coming apart.
Towards the end of my studying time, Lamello biscuit joiners started gaining popularity, and by the 1990's biscuits had become the go-to method for joining cabinets. Many cabinet shops had stationary mortisers for floating tenons for stronger joints.
Then Festool introduced the Domino into the US in the first years of the 21st century. It was a portable, accurate machine for installing floating tenons. This was a game changer. I was so impressed with Festool's innovation that when I opened TFWW, a center for hand tools, I decided to add Festool to the mix. Over the years as a Festool dealer and user my faith in the system hasn't been challenged. We routinely use Dominos in our own shop for all sorts of construction. There are cases where manually cutting a mortise is easier, usually when working with bizarro angles, and there is the satisfaction of chopping a mortise by hand. The system isn't cheap, either. But for me, the Domino me is an enabler of projects I would not ordinarily have the time for.
Magnification
I am getting older - better than the alternative - and for the past five years or so I haven't been able to see detail. My eyesight has been bad since third grade, but worsened with time. About ten years ago I started wearing continuous bifocals for reading. I also have a pair of computer glasses for focusing on my computer screen and reading . Close-up work become impossible until I re-discovered what everyone else in the same situation had already re-discovered: Magnification! Specifically, the Optivisor, which we now stock. They are surprisingly comfortable. I use a number 5 (2 1/2x magnification) with a headlamp. It makes a huge difference for small work. For just doing things like sharpening a saw, lesser magnification a #2 (which only magnifices 1.5x which isn't much at all) is a game changer for me. The lower magnification gives me a greater working distance which is nice. I wear them over my glasses. They are US-made and are of sufficiently high quality so I don't get eyestrain. I don't know what I would do without them. The game changing was especially sweet because between the time I noticed I could not do close work anymore and getting the Optivior, I went through an unhappy period of thinking that my woodworking days were behind me. I live in an apartment and I don't really need more furniture, but carving and miniatures have always held an attraction. I had been hoping that I would become good enough at relief carving to really enjoy the results of doing it - something not possible without magnification.
My first encounter with shellac was with a small bottle of hobby store shellac that might have been purchased during the Eisenhower administration. When I tried to use it during the Johnson administration it seemed to just lie there and not dry at all. Shellac was a mystery until maybe ten years ago. At that time I started understanding the difference between what you got in bottles pre-mixed, and what you could do if you mixed up shellac flakes with good alcohol yourself. While I had seen French polish in museums, it was only then that I saw fellow woodworkers finish their work with French polish. For the first time I really understood how wonderful shellac could be. Since that time I basically have three go-to finishes. Finishing oil, for anything that I want a matte finish on and anything walnut. Polyurethane from a can, for anything I just need to keep clean of fingerprints and I don't care about. And fresh shellac, mixed up from de-waxed shellac flakes as needed, French polished, or just brushed on and rubbed out. That's my classy finish. I still love my oil finishes but a shellac finish is just classier on so many levels.
That's all for now. More to come next time. What are your gamechangers? |
I resist the Domino because it is so expensive for my needs as a hobbyist.
I am just back from visiting Japan. I was amazed that the wood in all older houses was not always protected but ratera left in its natural state. It left me reassessing my own finishes.
I'm enjoying this series of posts.
Thank you for emphasizing the value of good magnification for certain work. No one balks at using a wrench to increase mechanical leverage to tighten a fastener, yet many woodworkers avoid aids to increase visual "leverage," which can improve the quality of their work.
For practical advice from a professional (me) on how to choose Optivisors: http://www.rpwoodwork.com/blog/2015/06/06/seeing-better-for-woodworking-a-guide-choosing-headband-magnifiers/ There are actually a lot of technical matters that come into play but I've boiled it down to simple practical guidelines.
Rob